If you read 10 articles about today’s most popular packaging and labeling trends, you’ll likely be faced with (at least) 10 different opinions. To make an informed decision, it’s important to understand how each affects your Plate Room/Plate Department – if at all.
As a software company dedicated to automating the pre-press and plate-making processes for flexo label and packaging printers, we’ve seen firsthand the transformation taking place in the industry. So, let’s dive in and explore how these trends are shaking up your Plate Room.
In an era where information is abundant, it’s no surprise that the packaging and labeling landscape is constantly shifting. Sustainability, smart packaging, molded fiber packaging, personalization, and versioning are just a few of the trends that have captured the industry’s attention.
But how do these trends influence your plate-making process? Let’s break it down.
1.
Sustainability: The Green Revolution
Sustainability is no longer just a buzzword; it’s a driving force behind packaging decisions. Sustainable practices may require special inks, substrates, or even reducing the packaging itself, leading to the need for special dies. Monitoring the lifecycle, mileage, and condition of plates or dies becomes crucial in this context.
2.
Bolder Colors and Special Embellishments
The demand for eye-catching designs featuring bolder and more saturated colors, foil stamping, and raised 2D effects is on the rise. This can result in heavier ink coverage on specific parts of a plate. Fine details in hand-drawn illustrations are becoming popular, necessitating clear plate reproduction.
3.
Regulatory Compliance and Multilingual Packaging
Global markets mean adhering to various regulations and languages. Tiny type as small as 4, 5, or 6 points must be legible, and the same regulatory text may occupy varying amounts of space on a package. This complexity leads to the creation of multiple plate versions, increasing the risk of human errors.
The crux of the matter is that each of these trends affects the printing plate, and as label and packaging designs become more intricate, Plate Room/Platemaking Departments must monitor plate conditions and mileage meticulously to ensure top-notch print quality during press runs.
As complexities mount, it’s crucial for printers to have control over all the tools used in the printing process, especially plates. The answer? Full automation. This approach provides real-time control and instant visibility over all printing tools and processes, minimizing the chances of costly reprints, missed deadlines, and, most importantly, keeping your customers happy.
With the advent of faster and more automated flexo and offset presses, the Plate Room/Platemaking Department now faces immense pressure to produce flawless plates well in advance of the run. The expectation is that jobs once printed digitally or on offset presses will exhibit the same quality when printed on flexo presses. Consequently, there’s an increased demand for a reliable platemaking process and ‘smart’ plate processing equipment with high uptime and easy maintenance.
To thrive in this ever-changing environment, Plate Room/Platemaking Departments must embrace automation and invest in the right tools and processes. By doing so, they can ensure top-quality prints, meet tight deadlines, and keep both brand owners and customers happy. It’s time to adapt, innovate, and stay ahead of the game in the world of label and packaging printing.
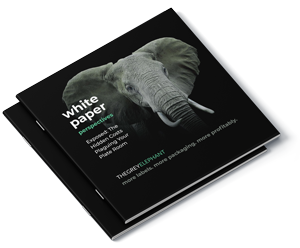